Learning Lean in the Field: An Asst. PM Earns Sweat Equity, Knowledge and Respect
A perspective from Michael Tourgee
While a degree provides a great start, there is no education better than hands on learning – especially when it involves getting a little dirty and putting in some sweat equity.
Michael Tourgee was introduced to KHS&S as a college intern which ignited his desire to earn a Master’s Degree in Construction Management. During his internship, he shadowed project supervisors to better understand the construction process and products. Now with nearly four years as a KHS&S project engineer, he requested to go back out on a job site to better develop his “field eyes.”
“It’s an opportunity to learn from the more experienced and discover tips and techniques to improve my estimating and project support skills that I may not recognize being in the office,” said Tourgee.
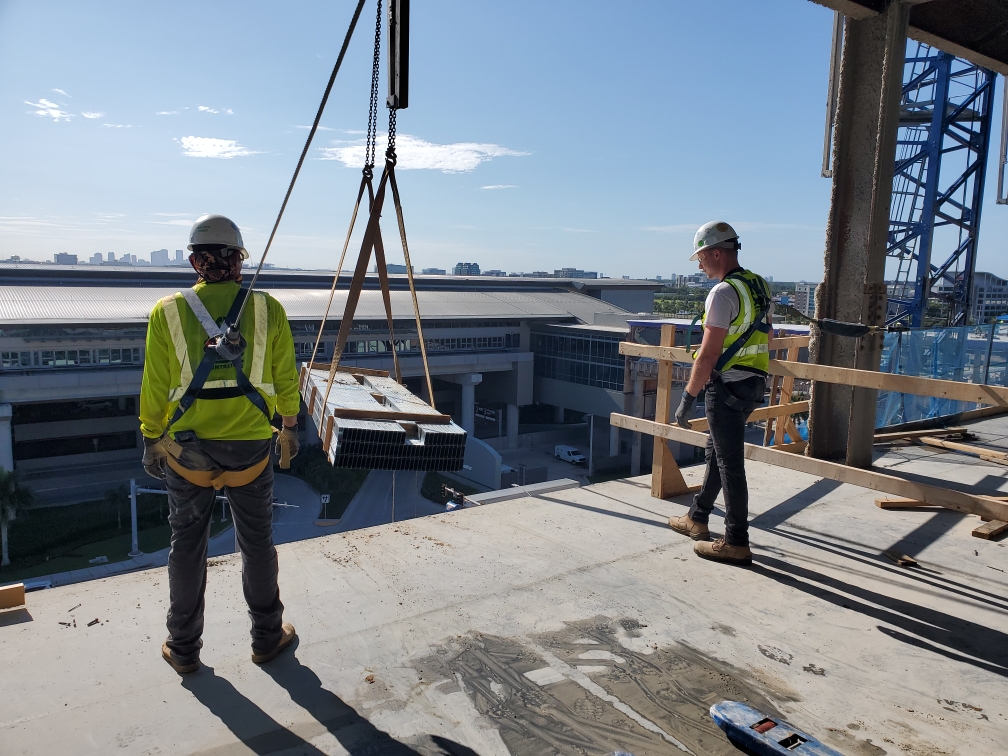
Having completed Lean training as well as attending the LCI conference, Tourgee wanted to experience Lean in action. So, how did the Lean training in the classroom translate to the field? Tourgee describes it as a real “eyebrow raiser.”
“In training, we’re typically working with perfect conditions such as all walls being the same, when in reality, the concrete or beams may be slightly off and so many more construction challenges will arise,” Tourgee said.
He splits his time between the Tampa office and SkyCenter One at Tampa International Airport. The site was selected as it represents a typical project Tourgee would be estimating and supporting. Reporting to Abraham Valentin, project superintendent, he participates in daily huddles and then heads to the field to work on anything from framing soffits to hanging walls.
To record his experience, Tourgee keeps a daily journal to recap techniques, tips and lessons learned that will help him when he returns to the office. Here are some highlights from his time in the field:
What job did he like performing: Framing soffits appeals to my Lego mentality. As a numbers person, I like the precision required in making cuts and ensuring everything is level and a perfect fit.
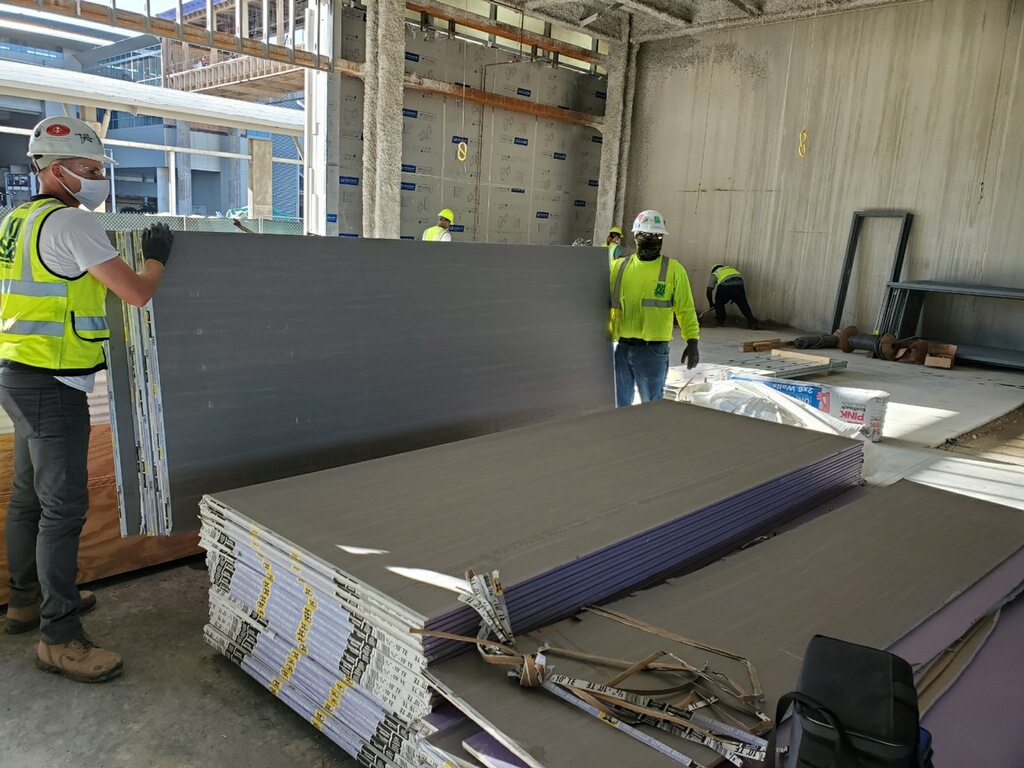
How did his Lean knowledge benefit a specific assignment: While framing, two guys were on the lift and we were having to go up and down multiple times to get material as it was being cut. We stopped, reassessed, cut all the studs at once and stocked the lift to reduce trips. It’s all about keeping the man on the wall longer.
What makes him proud to work for KHS&S: The general contractor often recognizes the team and encourages others to follow KHS&S practices such as planning deliveries well in advance or having materials placed where work is being completed. KHS&S does a great job leading by example. The Lean culture is so engrained in our people that it pushes other trades to complete work on schedule.
What he has appreciated most: Everyone is always teaching and learning. A 25-year veteran passes on Lean techniques to the younger tradesman, while the person on the job for a year brings a new perspective on ways to improve efficiency.
Advice to others training in the field: To gain respect and increase your knowledge, don’t be afraid to get dirty. Go after it as hard as you can – even if it comes with a few scrapes and bruises. It requires a full-force attitude.
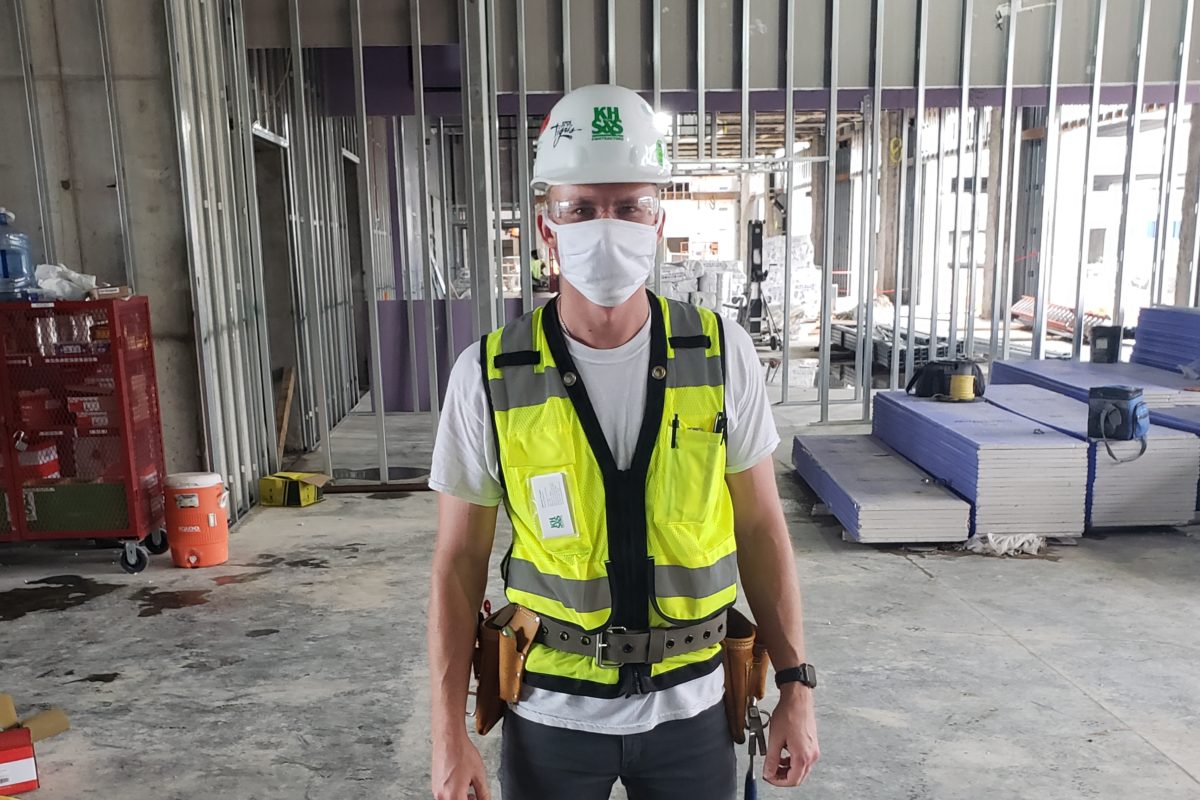